Development status of wear-resistant belt materials for oil drill pipe joints
White Paper
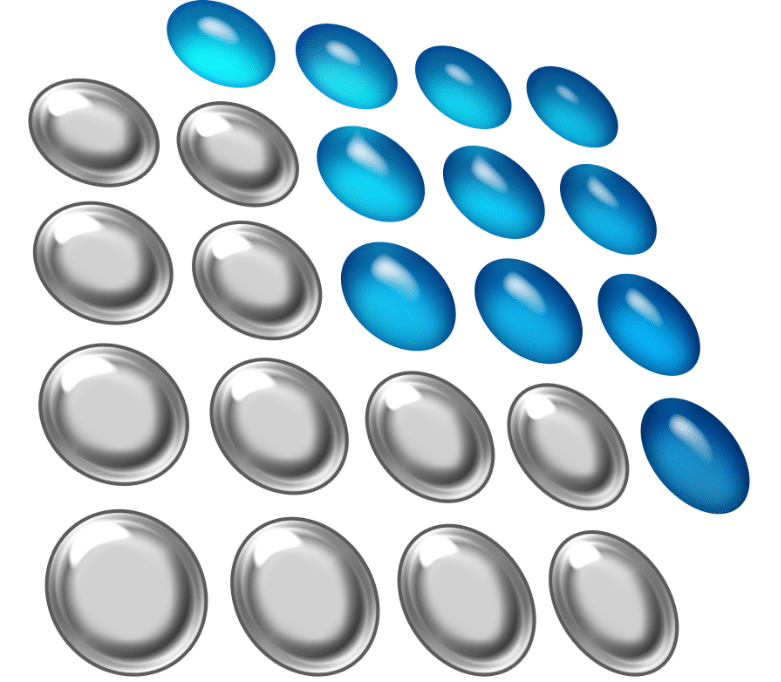
With the continuous development of drilling technology for oil and gas field exploration and development, the application of complex wellbore structures such as deep wells, extended-reach wells, horizontal wells, multi-lateral wells, and large-deviated wells is becoming more and more extensive, and the formation structure in the process of oil drilling is becoming more and more complex, among which the number of strong abrasive formations has increased sharply, which puts forward higher requirements for the anti-wear and anti-friction characteristics of drill pipes.
The drill pipe joint is an important part of the drill pipe, which adopts a large wall thickness, and the outer diameter of the joint is larger than the outer diameter of the drill pipe body, which is used to connect the drill pipe to form a pipe string. In the process of drilling, when the inclination angle of the well is large or the drill string is subjected to lateral force, the drill pipe joint is in contact with the borehole wall or the inner wall of the casing, resulting in two-way wear of the drill pipe joint and the casing wall. At present, the anti-wear technology of drill pipe joints mainly includes: drill pipe joint wear-resistant belt, drill pipe rubber guard, rotating drill string joint, drill pipe protector, etc., among which the drill pipe joint wear-resistant belt is easy to operate and has the best effect, which is the most effective measure to reduce the wear of drill pipe and casing.
In the formation with strong abrasiveness, the wear-resistant belt of the conventional material drill pipe joint is seriously worn, which significantly reduces the service life of the drill pipe, increases the downhole accidents such as expansion buckle, tripping and broken drill pipe significantly, increases the repair rate of the drill pipe joint sharply, and increases the maintenance cost and drill pipe scrap sharply. In wells with complex wellbore structures, due to the many layers of casing and the serious deformation and bending of the drill string, the wear band of the conventional material drill pipe joint wears a large amount of casing, which cannot play the role of anti-wear protection.
With the gradual solution of the problems of drill pipe joint wear-resistant belt materials in field applications, new wear-resistant belt materials have been continuously introduced, and the material varieties of wear-resistant belts have become more and more abundant. This paper comprehensively reviews the development and application of wear band materials for drill pipe joints, which is of great significance for promoting the further improvement of the wear band technology of drill pipe joints.
- Requirements for material properties of drill pipe joint wear-resistant belts
Wear bands are a hardened layer fixed to the drill pipe joint, drill collar or weighted drill pipe. This hardened layer isolates the drill pipe joint from the casing or borehole wall and has a certain hardness to protect the drill pipe joint. The friction factor is lower than that of the drill pipe joint, which reduces wear on the casing. Wear bands aAre usually fixed to the end of the female joint of the drill pipe using an inert gas welding process.
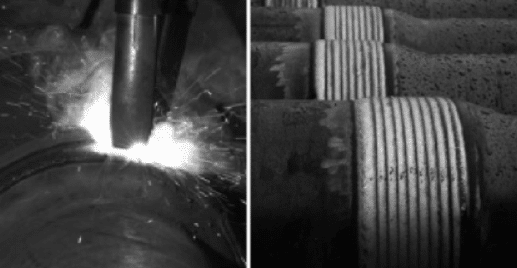
Drill pipe joint wear belt appeared as early as the 30s of the 20th century, and was mainly used to protect drill pipe and other tools from abrasive wear and prolong service life in the early days. However, with the increase of complex wells such as extended-reach wells, horizontal wells, and high-temperature and high-pressure wells, the wear belt of the drill pipe joint wears out the casing seriously, and the casing failure accident increases, causing millions of dollars in maintenance, sidetrack and even full well scrapping costs to the oilfield every year. Since then, the new wear belt has focused on reducing the wear and tear of the drill string on the casing during rotary drilling and lifting, while sacrificing the protective effect of the wear belt on the drill pipe joint. In the mid-90s of the 20th century, due to the increase in the price, transportation time and transportation cost of drill pipe, people began to pay new attention to the protective effect of wear strips on drill pipes, and new “casing-friendly” wear belts were introduced into the drilling industry. After nearly 20 years of development, the wear band material has been able to effectively solve the wear problem of casing, riser and drill pipe joint.
The drill pipe joint wear band material must have 3 properties at the same time:
1) Abrasion resistance. The ability of the material’s wear band to resist formation rock abrasion in the open hole wall.
2) Anti-friction. The material wear band can control its wear on the casing within an acceptable range.
3) Friction factor. The friction factor of a certain material wear-resistant belt is closely related to the advantages and disadvantages of its friction reduction at first, the smaller the friction factor, the smaller the friction between the casing and the casing, and the less wear caused to the casing, in addition, the low friction factor can greatly reduce the torque of the drill string and the resistance of the drill string, which is conducive to reducing the loss of energy and saving costs.
- The development status of foreign wear-resistant belt materials
The development process of drill pipe joint wear band material is divided into two stages: the first stage is the tungsten carbide material stage, from the 30s to the early 90s of the 20th century, and the second stage is the “casing-friendly” material stage, from the 90s of the 20th century to the present.
2.1 Tungsten carbide material stage
Tungsten carbide material wear band was invented and put into the market by Hughes Tools Company in the 30s of the 20th century, mainly used to prevent the abrasive wear of the drill pipe joint in the open hole section and improve the service life of the drill pipe.
This wear strip is composed of a mild steel matrix and tungsten carbide particles, which are evenly distributed into the molten steel molten pool in a molten state during the welding process of the wear band. The wear band of this material can prevent the drill pipe joint from contacting the open hole wall and is a very effective way to protect the drill pipe joint when most of the shallow wells (<1500m) and vertical wells (well deviation is less than 2°) in the early stage of the oilfield industry.
However, as well structures become more and more complex, well depths become deeper and deeper, and well inclination angles become larger and larger worldwide, people have begun to pay attention to the problem of casing failure caused by tungsten carbide wear belts. The experimental study confirms that in the process of rotary drilling and lifting, because the matrix alloy of this wear-resistant belt is relatively soft, the cemented carbide particles embedded in it are quickly exposed, which causes serious abrasive wear on the casing wall and eventually leads to the failure of the casing.
After that, in order to avoid the loss caused by casing failure, the oilfield company decided to stop using tungsten carbide wear belts, and only allowed the use of smooth drill pipes without wear belts or other anti-wear technologies (such as drill pipe protectors, rotary drill string joints, anti-deflection wear devices, etc.). When using light drill pipe, the life of the drill pipe is greatly reduced, and the wear problem of the casing can not be improved, this practice was quickly prohibited; other anti-wear technologies can reduce the wear of the casing to a certain extent, but generally face the problems of high cost, complex structure, difficult installation, low life, easy to cause downhole accidents, etc.
Therefore, the major technical service companies began to develop new materials to replace cemented carbide, the general characteristics of these materials are low friction factor, small wear on the casing, high hardness, can protect the drill pipe joint to a certain extent, after which the development of the drill pipe joint wear belt material has entered the “casing-friendly” material stage.
2.2 “Casing-friendly” material stage
The “casing-friendly” material has a low friction factor, and the friction and frictional heat generated by the wear band when it comes into contact with the inner wall of the casing, resulting in low casing wear. There are two main types of “casing-friendly” materials: one is an “amorphous” material wear belt, and the other is a “crystalline” material wear belt. A crystalline material is a material in which the arrangement of atoms inside the material follows certain rules. Conversely, materials with irregular internal atomic arrangements are called amorphous materials.
2.2.1 “Amorphous” material wear belt
In 1990, Liquidmetal Technology Co., Ltd. developed a chromium alloy wear band material called Armacorm, which is an “amorphous” (work hardening) material, the microstructure of the alloy material has no grain boundaries, and is distributed in a single atomic structure, this metal structure is characterized by a very low friction factor, so the wear of the casing is very small, which can greatly reduce the wear of the casing, and is the first “casing-friendly” Wear band material makes a big step forward in wear band technology. The disadvantage of this wear tape material is that the wear resistance is insufficient, because the “amorphous” wear belt only has a very thin amorphous protective (work hardening) layer only a few microns thick, which has poor ability to withstand high-pressure wear and cannot protect the drill pipe joint well.
2.2.2 “Crystalline” material wear belt
At the end of 1992, Anke Technology Co., Ltd. developed a new generation of chromium carbide alloy wear-resistant belt ARNCO200XT. This material wear band can effectively reduce the wear of the casing, and can ensure the durability of the drill pipe joint in the open hole section to minimize the wear of the drill pipe joint. However ARNCO200XT it is easy to produce microcracks during the welding process, although it has no effect during use, but all the cracked parts should be removed when re-welding. Subsequently, Acro has successively developed ARNCO100XT, ARNCO300XT, ARNCO150XT and ARNCO350XT drill pipe joint wear-resistant belt materials, overcoming the ARNCO200XT problems. ARNCO200XT was the first product, and production of this product was discontinued at the end of 2006.
Contact Us
For inquiries or to discuss your specific needs, please contact us.